The Future Of Electromagnetic Dent Removal
The Future Of Electromagnetic Dent Removal
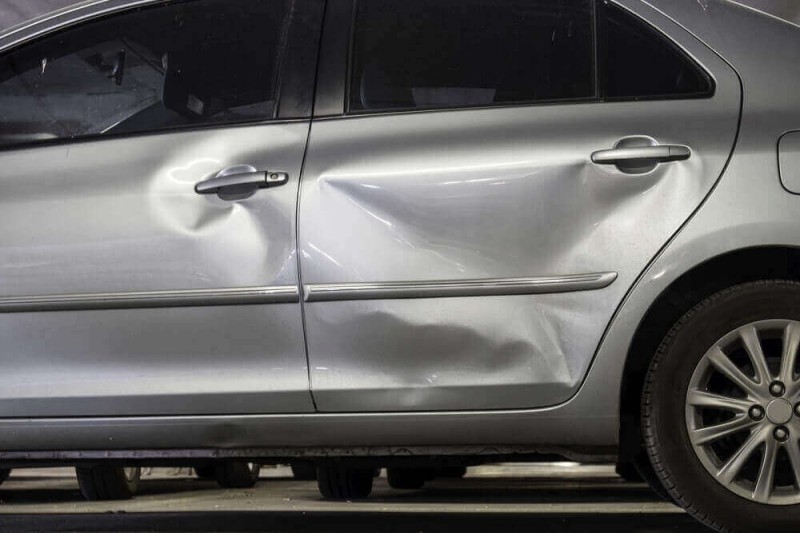
For several years electromagnetic dent removal has been a viable process for aircraft. The materials used in the manufacture of modern planes are the perfect candidates for this unique practice. It isn't as intrusive as other measures and can be used on a fully fueled aircraft without worry of combustion or damaging the avionics. In many ways it would be the perfect solution for the automotive industry, but the technological advancements necessary to make it work just haven't manifested. This is unfortunate to collision centers such as our partners at Collision Works Of Wichita Downtown here in Wichita, KS as well as other body shops across the globe. If perfected, it could be the best solution for many customers.
The process of removing dents with nothing but a strong electromagnetic field is pretty amazing. It works on any material that can conduct an electric charge, but aluminum seems to be the best candidate due to its structure and resilience. The electromagnetic dent removal (EDR) machinery generates a fluctuating magnetic field. This creates a current that flows through the material used. At a specific point in the field's fluctuation, the wavelength is flattened. The result is an outward blow that is pinpointed on the dent, pushing it outward. It may take a few attempts, but overall it has been proven to be very effective.
It's especially useful in cases where the other side of the material is inaccessible and typically leaves the paint intact. For planes it's amazing. Dents that require a full teardown to fix could take weeks to repair. With EDR it can take minutes to hours. Why then is it not being used in the automotive industry?
There are a few reasons. The first is portability. The power supply requires a forklift to maneuver. It's both large and heavy. It's also prohibitively expensive. The average model will run you about half a million dollars. It takes over a year to deliver a completed unit from the most reliable manufacturer. Lastly, no units are manufactured to the specifications for automobiles. The materials used in aircraft manufacturing is wildly different from those used in the automotive industry.
That leaves us with the question: What would it take to get a usable EDR in our body shops? In theory it's simple. We need a portable unit that is calibrated toward automotive body materials. In reality it's a little more difficult.
Different automotive parts are made from different materials. They vary from manufacturer to manufacturer and have different densities as well as compositions.
This is on top of the issue of power generation. Scaling down a 1,500 lb. power generator into something you can cart around the shop isn't going to happen overnight.
Perhaps if research and the corresponding funding were turned in the right direction now, we may make strides in the coming years in the right direction. For now we can only wait until our reality catches up to our aspirations.
Written By: Todd Hendrickson
Source: electroimpact.com
Social